
Metal surfaces consist of many different crystals and grains, some of which are less chemically stable than others. Targeted etching can remove these unstable particles from the surface of a metal, creating a three-dimensional surface structure that can support new bonding methods. This changes the properties of the surface, but not of the metal as a whole. Due to the etching, the treated surface visibly becomes matte. Because the etching is only 10µm to 20µm deep – a layer as thin as 1/4 the diameter of human hair – a research team at Kiel University, Kiel, Germany, has named the process nanoscale-sculpturing.
“If, for example, we treat a metal with sandpaper, we also achieve a noticeable change in appearance, but this is only two-dimensional, and does not change the characteristics of the surface,” explains Dr. Mark-Daniel Gerngross of the research team on materials sciences from Kiel.
The etching process creates a 3D-structure with tiny hooks. If a bonding polymer is then applied between two treated metals, the surfaces interlock with each other in all directions like a three-dimensional puzzle.
“These 3D puzzle connections are practically unbreakable. In our experiments, it was usually the metal or polymer that broke, but not the connection itself,” says Melike Baytekin-Gerngross, lead author of a publication describing the process.
It is through this nanoscale-sculpturing process that metals – such as aluminum, titanium, or zinc – can permanently be joined with nearly all other materials, becoming water-repellent and improving their biocompatibility. The potential spectrum of applications of these super connections ranges from safer implants in medical technology to metalwork.
“We have now applied a technology to metals that was previously only known from semiconductors. To use this process in such a way is completely new,” says co-author Dr. Jürgen Carstensen.

In the process, the surface of a metal is converted into a semiconductor, which can be chemically etched and modified as desired.
“As such, we have developed a process which, unlike other etching processes, does not damage the metals or affect their stability,” says Professor Rainer Adelung, head of the functional nanomaterials team at the Institute for Materials Science. “We can permanently connect metals which could previously not be directly joined, such as copper and aluminum.”
Potentially limitless applications
“The range of potential applications is extremely broad, from metalworking industries such as ship-building or aviation, to printing technology and fire protection, right through to medical applications,” Gerngross says.
Because the nanoscale-sculpturing process not only creates a 3D surface structure, which can be purely physically bonded without chemicals, the targeted etching can also remove harmful particles from the surface, which is of particularly great interest in medical technology.
Titanium is often used for medical implants. To mechanically fix titanium in place, small quantities of aluminum are added. However, the aluminum can trigger undesirable side-effects in the body.
“With our process, we can remove aluminum particles from the surface layer, and thereby obtain a significantly purer surface, which is much more tolerable for the human body. Because we only etch the uppermost layer on a micrometer scale, the stability of the whole implant remains unaffected,” Carstensen notes.
Kiel University
www.uni-kiel.de
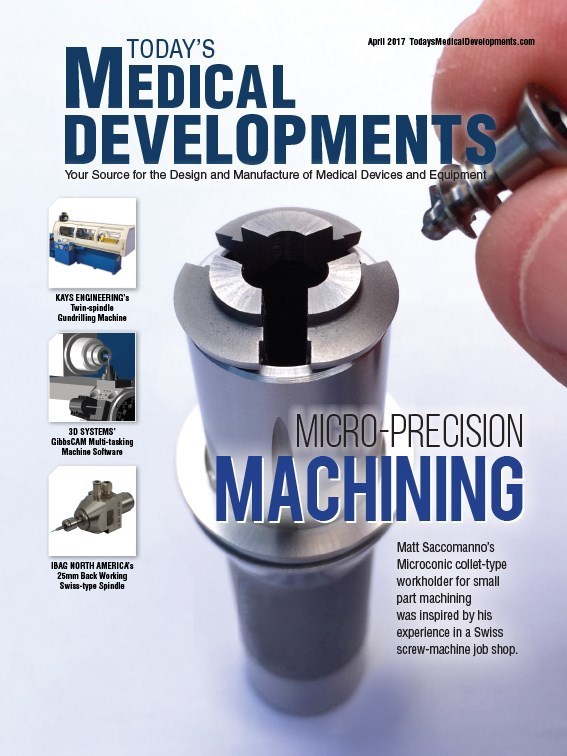
Explore the April 2017 Issue
Check out more from this issue and find you next story to read.
Latest from Today's Medical Developments
- UCIMU: Q1 2024, a downturn in the orders of machine tools
- #43 Manufacturing Matters - 2024 Spring Aerospace Industry Outlook with Richard Aboulafia
- Tsugami America’s Technical Center in Minnesota
- RobOps Copilot for AI-powered robot optimization
- US companies invest heavily in robots
- #34 Lunch + Learn Podcast - Cobots' potential to revolutionize aerospace manufacturing with Techman Robots
- Universal Robots announces seamless integration with Siemens PLCs
- This month's Manufacturing Lunch + Learn is May 16