
You’re sitting in the chair at the endodontist’s office. The pain has been so constant that when the words “root canal” come up, it sounds like relief. Looking at the array of instruments about to be used, you see dental burs (bits) for drilling and grinding, an endodontic file, and a root canal reamer. First, you hope the tools were manufactured to precise specifications, so your procedure goes as smoothly and quickly as possible. More important, you hope the tools are sharp – a sharp bur will cut quickly and cleanly, allowing the surgeon to precisely target damaged tissue and minimize the amount of pain you’ll face.
Considering these dental tools are micro-sized – typically dental burs are 0.5mm in diameter while endodontic files can have a tip as small as 0.0015" (0.0381mm) in diameter – toolmakers need the ability to inspect them in high-resolution to ensure specifications are met. And, whenever you’re talking medical manufacturing, precision, repeatability, and traceability are must-haves.
Micro tools tend to be fragile, so breakage can be a concern in inspection, making the use of a contactless measurement system necessary. Comparators or other projector-type devices are often used for this, but there are other options to consider.
Michael Stepke, product specialist for inspection machines at Zoller Inc., suggests the pomBasicMicro, one of the process-oriented measurement and inspection systems in Zoller’s pom group – others are the pomBasic and the pomSkpGo.
The pomBasicMicro has found its niche with medical manufacturing.
Medical manufacturers are not always willing to discuss success with a new process, but Stepke was more than willing to explain some of the advantages it brings to production.
“Zoller’s pomBasicMicro is a toolmaker’s microscope that eliminates the need for optical comparators, providing greater precision and more usable data. Sitting on the shop floor, next to the machine, the system allows tool makers to quickly qualify to specification by delivering fast, microscopic views of the required geometries on the tools,” Stepke says.
Edge-detection, illumination
Grinding machine operators can verify initial tool setup based on user selections or according to directions on the device screen. In the latter case, the measurement sequence is initiated by the push of a button. The system will automatically start a macro, guiding the user through the measuring process. Making the pomBasic even more user-independent is the fact that the system is capable of automatic edge detection supported by automatic lighting and illumination. All accumulating data can be recorded in the background, making it available to statistical process control (SPC) systems. The result – an economic, high-speed, compact, and user-independent unit that documents results for traceability. Reduced downtime is a win for users, Stepke explains.
Toolmaker’s microscope
The system’s pomColorCam features a 12x zoom macro lens, 0.5mm to 6.0mm field of view (FOV), an operating distance of 50mm, with 350x maximum magnification. Manual axis adjustment in X and Y is at a resolution of 0.001mm.
“Then there’s the lighting aspect of the system,” Stepke notes. “Anyone who is a toolmaker using inspection microscopes has struggled with illumination. But it’s critical. Zoller’s 8-segmented LED ring light enables illuminating OD and end view by activating different segments for proper reflection. There’s also the option of LED spotlights in red and white, and an LED-illuminated light tube that homogenizes the display of facets and angles of the tool.
Proper lighting enhances the inspection process, delivers accuracy and repeatability, and supports precise automatic detection of cutting edges. The light options offered with the pomBasic micro are currently the best in the market.”
Image processing takes place using Zoller’s Pilot 3.0 platform. Freely programmable and guided measuring sequence macros allow less-experienced operators to measure proficiently. Another benefit of macros is consistency between multiple operators. Verification with macros automatically delivers saved data for traceability and SPC, as required in medical manufacturing. A report with any variations of tolerance and a go/no-go sign is saved with each job. The macros are shared through a single source database to multiple machines. Data is secured through detailed user management.



Overlays
A favorite feature is the transparent overlay of prerecorded master images with the live image of the new tool. This function is extremely lean and user-friendly. Digital DXF overlay is also included.
Fixturing, options, solutions
Inspecting micro-geometries and analyzing the smallest details demands accurate holding fixtures. According to Stepke, fixturing provided for micro-tools is ergonomic and quick to change. Fixturing examples are V-block and St. Mary’s centerless gages.
The system’s manual swiveling table enables universal clamping of these various tool holders, for easy fixturing and positioning. The 3 x 90° indexing can be variably adjusted to measure at both sides of the OD and the end of the tools (±120°), with the option of precisely holding an angular position with the use of spindle clamping.

An optional digital rotary encoder (ROD) is integrated into the swiveling table, allowing the readout to be displayed on-screen for fast and accurate positioning.
Also available with the system is the reGrind software module. Worn tools on a robot pallet are inspected in succession for wear. After completion of measuring tools on the pallet, the wear offset for each tool is transferred, typically to a 5-axis tool grinder, via post processor. Time and money is saved because regrinding is only done on actual tool-specific wear dimensions, and pallets are prepared beforehand maximizing machine output.
Stepke highlighted why medical manufacturers are implementing the pomBasic on the shop floor. “Previously, it took longer to inspect these micro-tools. The pomBasic systems, especially the pomBasicMicro for medical work, efficiently guides operators, delivering repeatable, consistent results with maximum precision and traceability from a user-friendly inspection system.”
Zoller Inc.
www.zoller-usa.com
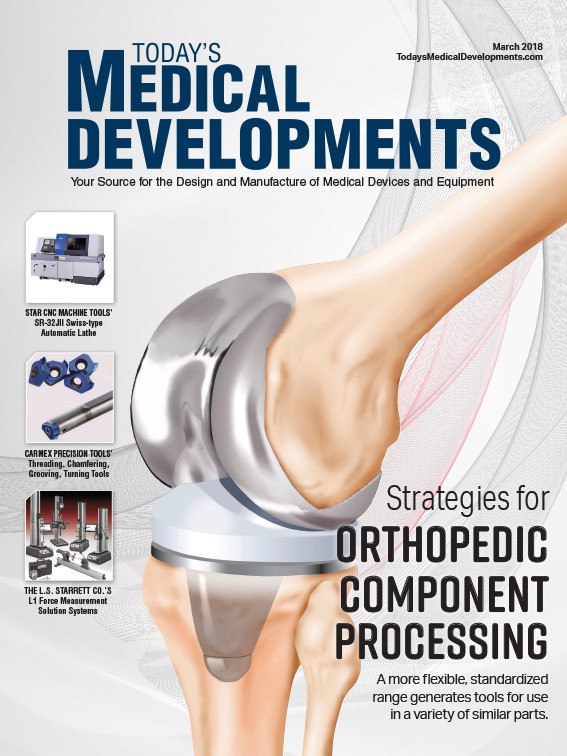
Explore the March 2018 Issue
Check out more from this issue and find you next story to read.
Latest from Today's Medical Developments
- Tsugami America’s Technical Center in Minnesota
- RobOps Copilot for AI-powered robot optimization
- US companies invest heavily in robots
- #34 Lunch + Learn Podcast - Cobots' potential to revolutionize aerospace manufacturing with Techman Robots
- Universal Robots announces seamless integration with Siemens PLCs
- This month's Manufacturing Lunch + Learn is May 16
- Ultrahuman wearable technology
- Additive Manufacturing for Aircraft Cockpit Interior Components