On a two-wire device, since there is no grounding pin on the NEMA plug, high voltage could be present to the operator.
Safety agencies require a Dielectric Withstand (Hipot) and ground continuity test on every finished product. Manufacturers need to design a Hipot test station that will conduct the test efficiently, while keeping personnel safe. Since the Dielectric Withstand test requires the use of high voltages, design of this station is important.
There are two tests conducted for the agencies. First is the Dielectric Withstand (Hipot) test, which ensures that primary main components are isolated from safety ground. Second is the ground continuity test, which ensures connection of the building ground to the chassis of the product. Passage of this test demonstrates that primary wiring faults are unlikely and, if they do occur, the building breaker will operate to keep users safe.
The Dielectric Withstand test involves applying a high potential between current carrying primary parts and the safety ground of the appliance. The high voltages involved in this test are dangerous, and the manufacturer must take steps to protect test personnel conducting the dielectric testing.
Designed to protect the operator from shock, additional design considerations of Hipot test stations must also address the following:
- Hipot tester design and building safety ground issues;
- Personnel training;
- Test station location and design;
- Non-conducting barriers;
- Interlocks; and
- Periodic function checks.
Inherent Safety
Hipot testers have a high voltage output and a return lead – first bolted to the chassis, and then bolted to the green wire of its power supply cord – which is the primary line of defense against operator shock. The wall outlet being used to power the Hipot tester must be the three wire (NEMA 15P) type.
The safety ground is what keeps personnel safe. If the equipment and Hipot tester are correctly grounded, technicians will not receive a shock when touching the test setup, even in a failure condition. The Hipot tester return lead is what is grounding the chassis of the product, and keeping technicians safe from shock in the event of a Hipot test failure. If the building ground or the return lead is faulty, the grounding of the chassis of the product is incorrect, or not grounded, and is dangerous. Without a good ground connection, the Hipot tester may not recognize a fault, and high voltage could be present on the enclosure of the product for the duration of the test. In addition, the Hipot tester leakage current limit circuit will not work without a good ground. In this situation, bad products can appear to be passing a Hipot test.
Operator Safety
Connection of a Hipot tester to a properly grounded receptacle insures that conducting a Hipot test can be accomplished in a very safe manner. The operator clips a return lead to the chassis of the product, and plugs the product’s cord into the Hipot tester. The Hipot checks for continuity between the cord and the chassis to make sure the safety ground connection is acceptable. If the safety ground connection is bad, the Hipot test will not start. If the safety ground connection is good, then the chassis of the device under test holds at ground potential throughout the Hipot test, and the technicians are safe. Even if discovery of a fault occurs during the Hipot test, the voltage from the Hipot tester passes through the safety ground circuit to the building ground and the equipment will not pose a shock hazard.
Testing 2-Wire Products
Tests with products using a two-wire polarized plug, or products using a junction box for connection to building power (flying black, white, and green leads instead of a power supply cord), could expose the operator to high voltage. Two wire products do not possess a connection to a building ground and, therefore, they carry a greater shock hazard. Although the Hipot tester return lead will be connected to the chassis of the product, as standard, conducting of the ground continuity test cannot be accomplished. In addition, if the return lead is defective, or not properly connected, the product does not contain grounding and this carries a greater risk for producing a shock. There is no way for the Hipot tester to detect this problem, so training operators to make proper connections is necessary.
Flying Power Leads
In this case, application of high voltage is performed to both the white (neutral) and black (power) exposed leads. Operator training is necessary because of the amount of exposure of high voltage while conducting the test. Instructions should demonstrate how to make reliable connections to both the black and white wires, with the high voltage lead, and the best way to make the safety ground connection. A fixture, guards, or an interlocked door is a primary consideration in the protection of the operator from exposure to high voltage.
Personnel Training
Training must be more detailed than, “here is the button, push it, and stand back.” It should include:
- Proper operation of a Hipot tester;
- The hazards of high voltage; and
- Where high voltage is on the tester
Further points for training are:
- Proper connection of the ground lead; in certain configurations, the Hipot tester cannot test for a good ground before applying high voltage, so safe testing requires the operator’s ability to make a good ground connection.
- High voltage and return leads must remain connected until the Hipot meter reads zero volts. Disconnection of either lead before discharge of all voltage can leave voltage in the power supply of the device being tested, which may occur when operators are urged to complete testing as quickly as possible.
Location, Design
The test station should be marked, preventing untrained personnel from gaining access. A main power disconnect should also be installed and marked so anyone will be able to shut off the power to the designated area. Grounding of the power source, in accordance with NFPA codes is also required.
Make sure to use a non-conductive bench, not an ESD workstation, located in a large enough area to allow the operator room to distance themselves from the test in an emergency. Arrange the equipment on the bench in a logical fashion. If possible, arrange the Hipot tester so the operation buttons are at the far end of the test area – so the technician can operate the tester away from the device currently in test.
Non-Conducting Barriers
Non-conducting barriers should be considered for use between the operator and the device being tested. This can be something as simple as a plastic barrier, which is put in place after the electrical connections have been made, or, a more elaborate non-conductive enclosure with doors. A company, such as Industrial Automation Systems, is one that sets up more elaborate, non-conductive custom-designs. The doors of such an enclosure can be fitted with interlocks, preventing Hipot operation unless they are closed.
Interlocks, Warning Lights
Optionally, Hipot testers may be fitted with interlocks to prevent or stop high voltage flow when the circuit is broken. On the rear panel of the Hipot tester, two provided terminals are shorted together with a short jumper, for non-interlocked operation. Use of this requires that the manufacturer places safety switches in series with these terminals.
Periodic Function Checks
Finally, it is important to inspect the Hipot tester and cablesets on a regular basis. Function testers, such as Compliance West USA Model HTT-1, can test the safe operation of the Hipot tester quickly and efficiently, providing safety to the operator.
Compliance West U.S.A. Inc.
Del Mar, CA
compwest.com
Industrial Automation Systems
W. Boylston, MA
industrialautomationsystems.com
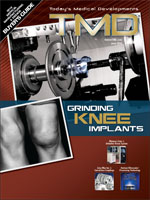
Explore the June 2010 Issue
Check out more from this issue and find you next story to read.
Latest from Today's Medical Developments
- Pump for kids’ failing hearts
- Flexiv Robotics’ collaboration with BlackBerry QNX
- #35 Lunch + Learn Podcast - How to use Autodesk Fusion with TATA Technologies
- mimic joins race to develop the first AI-driven cobot
- UPCOMING WEBINAR: Additive Manufacturing for Aircraft Cockpit Interior Components
- Better than graphene material development may improve implantable technology
- Still time to register for the May 16 Manufacturing Lunch + Learn
- Next generation of vision implants