As the market for orthopedic implants grows, year after year, so does the competition for manufacturing these components. At the same time, manufacturers are increasingly moving toward harder materials like cobalt chromium alloys for knees and other parts, which, at one time, machined with more ease. Meanwhile, the threat of government cost controls hangs over the industry. All of this adds up to an intense need to lower manufacturing costs – a need that is being answered with the NXis Ortho system.
By combining the machine design of the Helitronic Vision with proven coolant delivery and appropriate software, the NXis Ortho system is offering the orthopedic industry:
- Shorter cycle times;
- A better end-product that minimizes post-processing;
- Versatility for a wide variety of components; and
- Fast programming and setup
Just as important as the technology is customer support to help maximize up-time and readily adapt to changing requirements.
The wide variety and geometric complexity of orthopedic implants make them an ideal application for a 5-axis tool grinder with advanaced vision, such as the Walter Helitronic Vision. Applications Manager Simon Manns explains: “Our tool grinding customers consistently tell us the vision is 20% to 30% more productive than other machines, the reason it makes it ideal for orthopedic applications. For example, the machine’s 3D gantry offers excellent dampening properties for optimum surface finish, particularly when you are trying to achieve the fastest possible grinds. In addition, the design allows the user to grind in all four quadrants for geometric versatility.”
Linear, Direct Rotary Drive
The Helitronic Vision’s A and C rotary axes use gearless direct drive motors while X, Y, and Z use linear motors. There are no ball lead screws, gears, motor bearings, or backlash. Accuracy and smooth performance, plus the machine’s dampening characteristics, result in superior surface finishes and contour tolerances – up to two times more accurate than other CNC grinders – while the motors acceleration and speed minimizes non-grinding time.
Cool and Fast
The Vision applies a 32gpm (120 lpm) flow of coolant at 300psi through optimized compacted nozzles. The result is much better coolant placement than competing designs, yielding shorter cycle times and more accurate parts with minimal thermal distortion. “In fact,” says Manns, “you can touch the part immediately after the grind, and it is cool.” This is true even after heavy material removal like the condyle grind on a femoral knee. What is more, the excellent surface finish – with no burning – minimizes the need for post processing, further lowering the cost-per-part.
Easy, Fast, Versatile
Most orthopedic manufacturers design their parts using Siemens PLM NX or a similar CAD/CAM software. Then, they typically lose time as the manufacturing team determines how to make the component, often resulting in a redesign. Walter has developed a post-processor that goes directly from the part design to a complete 3D machine simulation and then to a machining program. This means design and manufacturing planning can occur in tandem, speeding the time from concept to market.
Applications Engineer, Robby Faulkner, explains that Walter “Uses full 3D solids based simulation that is driven from the actual G-code that runs the machine, so any operator can verify his machining paths and machine moves on a PC. He can be sure everything will work without interference problems because we are simulating everything, including things like dressers and the wheel shape. Competing systems do not do that, and they simulate every wheel or tool as a ballnose endmill.”
Walter’s man-machine interface also lets you run any Fanuc compliant G-code, freeing you to use other CAD/CAM packages. “The NXis Ortho software makes it easy to configure wheel dressing routines, after which the processor automatically generates the necessary NC code,” Mann adds. “The man-machine interface also automatically performs optimum dressing calculations and presents them as a guide. It is the most complete and user-friendly approach to CAD/CAM on a grinder that I have seen.”
Given the demands to both cut costs and constantly create competitive new implant designs, orthopedic manufacturers rely on quality machines, good service, and superior engineering support. As the U.S. team of software, design, and applications engineers developed the NXis Ortho system – together with input from the home office in Germany and participation by Siemens PLM and Fanuc engineers – a tool grinding machine is delivering the requirements manufacturers of implants have demanded.
United Grinding Technologies Inc.
Fredericksburg, VA
grinding.com
Siemens PLM Software
Plano, TX
plm.automation.siemens.com
Fanuc CNC America
Hoffman Estates, IL
fanuccncamerica.com
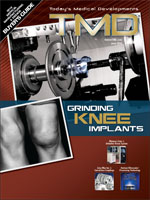
Explore the June 2010 Issue
Check out more from this issue and find you next story to read.
Latest from Today's Medical Developments
- Better than graphene material development may improve implantable technology
- Still time to register for the May 16 Manufacturing Lunch + Learn
- Next generation of vision implants
- UCIMU: Q1 2024, a downturn in the orders of machine tools
- #43 Manufacturing Matters - 2024 Spring Aerospace Industry Outlook with Richard Aboulafia
- Tsugami America’s Technical Center in Minnesota
- RobOps Copilot for AI-powered robot optimization
- Current products