Electromagnetic interference (EMI) between wireless devices and medical equipment is a growing concern in the health care industry. As wireless devices continue to proliferate in medical facilities, noise reduction, increased immunity to wireless RF emissions, and EMI mitigation need to be addressed and managed.
With this push toward more wireless devices within health care environments, EMI can have a detrimental effect on sensitive electronic components and circuits, endangering the health and lives of patients. There are many sources of EMI in the hospital environment, from electric motors to cellphones, computer circuits, power lines, and other medical systems such as electrosurgical units (ESU). Although regulations exist such as IEC 60601-1-2, these types of standards are developed by industry-specific organizations like the FCC and, specifically for medical devices, the FDA. These standards limit unnecessary electronic emissions and require immunity. In most cases, device manufacturers rely on shielding suppliers to have the technical capabilities and knowledge needed to suppress EMI.
Two approaches
There are two basic approaches for shielding electromagnetic emissions from a device or system as well as improving its immunity performance. One is shielding at the printed circuit-board (PCB) level utilizing proper design techniques. The second is to place the device or system in a shielded enclosure. This article discusses shielding products for use at both the PCB level (board level shielding – BLS) and at the system level (gasketing).
Board level shielding
A board level shield can be viewed as a five-sided can. Available in unlimited sizes, shapes, and heights, BLS goes around the component or circuit on the PCB that needs shielding. BLS restricts the amount of electromagnetic energy propagating between the source and a receptor to acceptable levels. When designing and manufacturing BLS, the following elements need to be considered for effective shielding.
Near-field effects: When the shield is in the near-field of the source, shielding performance is impacted by the frequency of the source, field configuration, position of the source, and distributed inductances and capacitances. In other words, the approach now becomes a coupling problem, not a radiated problem. Even when accounting for the apertures in a shield, calculating or estimating shielding effectiveness could still fall short of approximation. The coupling of the source to the shield, the effect of mutual coupling between elements, effect of the shield termination, and grounding technique all need to be accounted for. Currents diffusing through the shield, shield bends, and corners, and the resultant generated external voltages, also require consideration.
Layout and hole considerations: The effectiveness of BLS is highly dependent on the proper design of the PCB mounting area. Normally, the sixth side of this box will be a ground plane on the board. The number and spacing of traces, vias, and holes running from this shielded area to other board components can affect the effectiveness of BLS.
With higher frequencies and shorter wavelengths, the size and number of holes can become issues along with thermal effects. However, tempering this concern is the near-field effect. Capacitive and inductive coupling are more significant than aperture size for shielding.
Resonances: Another issue with higher frequencies is resonance effect – a consequence of self-resonance of various structures. A 2" x 1/2" enclosure resonates at a first-order mode of around 12GHz. Even weak coupling at these high frequencies can induce strong oscillations that can then couple to any other point in the enclosure.
Thermal management: Faster frequencies generate more heat. Therefore, thermal management is also a design factor. Thermal management can be achieved through using thermal pads and heat sink. Companies, such as Orbel, can assist with various design options that may be available.
Gasketing
Gasketing can maintain shielding effectiveness through proper seam treatment. Effects of seams, in general, account for most of the leakages in an enclosure design. The shielding effectiveness of a seam is dependent on materials, contact pressure, and surface area. Gaskets maintain conductive contact across mating surfaces. A solution to radiated problems is to make all seams of adjoining metal pieces continuous. If there is no continuity between metal pieces, a radiating aperture for RF current is created. This is where gasketing can be used.
Most gasket applications involve two types of forces – compression and shear. When installing gaskets under a flat cover panel in a compression configuration, pressure preserves the shielding effectiveness of the seam. In shear applications, a flange or channel arrangement preserves shielding effectiveness and no sliding action occurs.
Chosen based on specific shielding effectiveness requirements, application atmosphere, and spatial specifications, the use of both beryllium copper (BeCu) gaskets and metalized fabric gaskets can ensure maximum EMI compliance.
MBANs To foster the development and deployment of advanced wireless medical communications, the U.S. Federal Communications Commission (FCC) has modified its rules for medical body area networks (MBANs). MBANs are low-powered networks that transmit a range of patient data from multiple body-worn sensors to a control device. MBANs can be used to monitor patient vital signs in real time, providing advanced notice of potential problems. Because they are wireless, MBANs make it easier to move patients to and from different facility areas. The FCC originally allocated 40MHz of spectrum in the 2,360MHz to 2,400MHz band for MBAN use on a secondary basis in 2012. |
Beryllium copper: BeCu gaskets offer the highest level of attenuation across the widest frequency range and are useable in both compression and shear applications. Solid fingers have greater cross-sectional area, hence higher conductivity. In addition, the finger shape has the characteristics of an interconnecting ground plane with a large contact area. The inductance will therefore be low as well. The movement of the finger shape also provides a wiping action that aids in penetrating or removing any oxide buildup in the contact area. They are very forgiving to compression, meaning that it is very difficult to over-compress them causing compression set or breakage. Potential problem areas, depending on frequency range, are the slots between the fingers. At sufficiently high frequencies, these slots begin to permit RF energy transmission through the bounded slot configuration.
Metalized fabric: These gaskets are made of conductive fabric material over foam. Conductivity can be very low and offer very high attenuation – the level and matrix of the conductive particles used, and the compression force determine the amount of attenuation. These gaskets come in various styles and shapes (rectangular, square, D-shaped, bell-shaped, knife-shaped, etc.) that allow various compression ranges down to low values.
Design guidelines
Generally, either of these gasket types will provide effective shielding (mechanical characteristics and cost generally determine choice of gasket). The effectiveness of the gasket depends on using proper design guidelines.
Regardless of gasket type, important factors include RF impedance, material compatibility, corrosion control, gasket height, compression force, compressibility, compression range, compression set, and environment. For RF impedance control, high conductivity and low inductance is desired. It should not be a surprise that BeCu has the highest conductivity.
Corrosion: Corrosion can lead to reduced shielding effectiveness and can cause the gasket material to become insulative or create new problem frequencies through nonlinear mixing. There are two types of corrosion. Galvanic corrosion results from contact between two dissimilar metals in the presence of moisture. Electrolytic comes from current flow between two metals in the presence of an electrolyte. For commercial applications within controlled environments, galvanic-compatible materials are those within 0.5V to 0.6V.
Compressibility: The height or diameter of the gasket must be large enough to compensate for joint unevenness between mating surfaces for the force applied (compressibility). The difference between the minimum and maximum compressed gasket height should equal the joint unevenness.
Compression force: Compression force is the force required to achieve maximum shielding effectiveness. The higher the pressure or compression force, the lower the impedance. A minimum closure force is recommended to obtain low surface contact resistivity and effective shielding.
Minimum closure force is the pressure required to break through corrosive and oxide films to make a low-resistance contact. If insufficient pressure is applied to the seam, a high contact resistivity will exist and reduced shielding effectiveness will result. For a good joint seal, there needs to be low surface contact resistivity as well as low gasket resistivity (i.e., high gasket conductivity).
Orbel Corp.
www.orbel.com
About the author: Ed Nakauchi is a technical consultant to Orbel Corp. and can be reached at 610.829.5000.
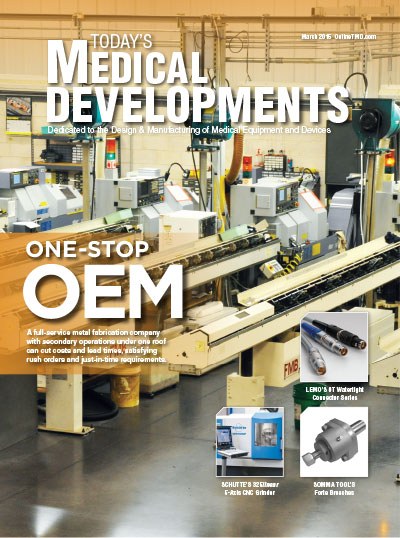
Explore the March 2015 Issue
Check out more from this issue and find you next story to read.
Latest from Today's Medical Developments
- Tsugami America’s Technical Center in Minnesota
- RobOps Copilot for AI-powered robot optimization
- US companies invest heavily in robots
- #34 Lunch + Learn Podcast - Cobots' potential to revolutionize aerospace manufacturing with Techman Robots
- Universal Robots announces seamless integration with Siemens PLCs
- This month's Manufacturing Lunch + Learn is May 16
- Ultrahuman wearable technology
- Additive Manufacturing for Aircraft Cockpit Interior Components