Formally known as DAMCO Inc., Plastic Molding Manufacturing started in 1968 as a plastic injection molder and single-source manufacturer for thermoplastic injection-molded components. During the past five years, the company has acquired four additional plastic companies to expand manufacturing across the United States, with multiple molding presses, automated machines, product development, and analysis capabilities.
The company’s 5,000ft2 cleanroom located in its Massachusetts facility specializes in medical and healthcare products with strict production requirements.
The facility’s recently added Allrounder 420C, two-shot injection molding machines from Arburg – for one-machine production of multiple components and materials – manufactures products such as enteral feeding devices, drug filtrations, insulin delivery devices, high volume disposable products, and housings and components.
Two-shot molding simplifies product designs, allowing product integrity improvements to benefit OEMs.
Two-shot molding
Plastic Molding Manufacturing’s cleanroom is equipped with standard horizontal clamp presses and a vertical rotary shuttle table for insert over-molding. The cleanroom is regulated by clean air flow patterns, continuous positive air pressure, and controlled temperature and humidity, which prevents the concentration of airborne particles and contaminates.
The company’s Connecticut facility has four two-shot machines currently in operation. Two-shot presses include family mold and two-part number capabilities to save on cost and production.
In all, the company has 82 injection molding machines, including five two-shot machines.
Allrounder applications
Multi-way valves for intravenous drip therapy are manufactured with Allrounder injection molding machines in large Class 8 cleanrooms. The valve systems are also assembled and put in their primary packaging. To ensure correct operation, stringent tolerances must be maintained during injection molding.
Dental drills made from PEEK only remove carious material, unlike their metal counterparts that can cut tooth enamel. The tiny drills are produced in a single step by Plastic Molding Manufacturing and similar companies for dental practices as cost-effective, ready-to-use, disposable items. An electric injection molding machine from Arburg’s Alldrive series ensures precision.
In docked cleanroom cells, a 6-axis robotic system places the dental drills in blister packs. These are individually perforated, printed, and removed from the cell in units of 10 by a conveyor belt. No refinishing or sterilization is required prior to use.
An Allrounder 370 injection molding machine produces two tiny drills in a cycle time of around 30 seconds. Because tolerances measured in the hundredth of a millimeter range have to be met, all the axes important for part quality, such as injection, dosage, and mold movements are driven electrically.
Two drills are automatically packaged simultaneously with the injection molding cycle. A flexible 6-axis robotic system moves to a number of positions within the room for this purpose. It removes the molded parts from the mold, sets them onto a cooling station, and then inserts them the right way around in the blister packaging.
The robotic system and packaging system are docked to the machine with a sealed guarding. Together with the clean air modules that cover the entire working area, a completely encapsulated cleanroom cell is created that meets the requirements of Cleanroom Class 7.
Hormone rings made from liquid silicone rubber (LSR) and used by women for HIV prevention can also be manufactured by Arburg’s Allrounder machines. The most stringent hygiene and product quality requirements must be met during production. The special advantage: before injection molding, an agent is mixed into the liquid silicone that provides protection against HIV.
A production cell built around an Allrounder 520A, produces LSR vaginal rings in large unit volumes. As the main contractor, Arburg bears the complete responsibility. The cleanroom application was developed in cooperation with Arburg partners Rico and 2KM.
Man over machine
Plastic Molding Manufacturing’s CEO, George Danis says reshoring has been key in the company’s growth.
“With our goals in reshoring manufacturing we have made appropriate adjustments in our capabilities and services to make sure we can provide stronger local services to exceed our customers’ expectations,” he says. “We plan to continue adding state-of-the-art machines and to improve our services to help bring manufacturing back to the United States, creating jobs to help improve the economy.”
Danis says the company implements continuous training and maturing to ensure its employees and equipment are providing customers with superior service. The company’s equipment choices coincide with each facility’s needs, updates, and manufacturing advancements.
“Training our employees to properly handle our machines is key to improving our capabilities,” Danis says. “We are looking to strengthen our skillsets to offer the knowledge, resources, and technology to help our customers’ projects be successful.”
Plastic Molding Manufacturing Inc.
www.plasticmoldingmfg.com
Arburg Inc.
www.arburg.com/us
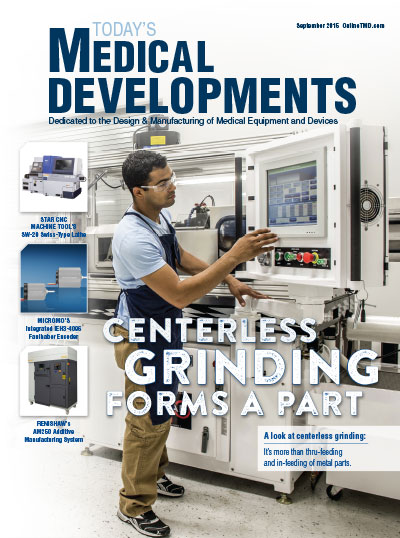
Explore the September 2015 Issue
Check out more from this issue and find you next story to read.
Latest from Today's Medical Developments
- mimic joins race to develop the first AI-driven cobot
- UPCOMING WEBINAR: Additive Manufacturing for Aircraft Cockpit Interior Components
- Better than graphene material development may improve implantable technology
- Still time to register for the May 16 Manufacturing Lunch + Learn
- Next generation of vision implants
- UCIMU: Q1 2024, a downturn in the orders of machine tools
- #43 Manufacturing Matters - 2024 Spring Aerospace Industry Outlook with Richard Aboulafia
- Tsugami America’s Technical Center in Minnesota