
GWS Tool Group
A medical device manufacturer was producing bone screws using a boring bar for internal threading being supplied from a European company, which meant the tools came from outside the United States. This led to challenges with the European supplier having inconsistent lead times averaging 10 to 12 weeks, along with severe quality concerns. In addition, the European boring bars demonstrated unreliable lifespans and unexpected breakdowns, leading to production halts and extensive quality inspections being constantly needed. To make matters worse, the customer had to use a time-consuming triangle tool holder, which finally pushed them to find a better alternative to their current high tool costs and manufacturing expenses.
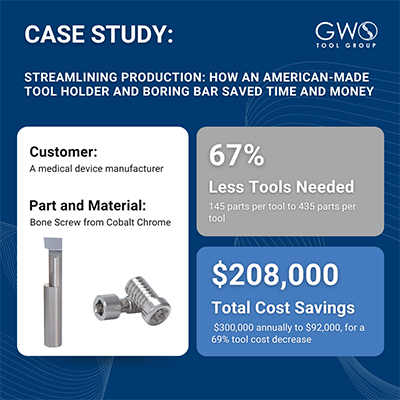
When the medical device manufacturer reached out to GWS Tool Group, the company had the perfect solutions for the medical device manufacturer’s problems. GWS introduced its quick-change tool holder system which switched them from their previous European triangle holder to our American-made custom round holder for a more universal application. In addition to the custom tool holder, we provided our solid carbide boring bar, which led to enhanced tool life and reduced changeover times. Transitioning from cobalt chrome to solid carbide tools increased tool life by 33%, resulting in 290 more screws being produced per tool. The reduction in tools required was staggering now, a 67% drop in tools required went from 7,100 annually to 2,365. This led to substantial annual tool cost savings totaling $208,000. In addition to the huge cost benefits, GWS ensured reliable lead times and consistent American-made tool performance, significantly improving the overall operational efficiency for the medical device manufacturer.
Get curated news on YOUR industry.
Enter your email to receive our newsletters.Latest from Today's Medical Developments
- Blum-Novotest opens new Competence Center in Erlanger, Kentucky
- HydroPlasma: The future of surface cleaning in high-tech industries
- Heule partners with Center for Machining Excellence
- Down the road: What really is next for electric vehicles?
- Driving successful medtech innovation
- Last call for July’s medical manufacturing Lunch + Learn!
- Transform What’s Possible with the Okuma MULTUS U3000
- Okuma: Extraordinary Starts Where Limits End